Material topic
- 17 Product safety and quality
Product quality and product safety
Lindt & Sprüngli is committed to a culture of quality. Our dedication to meeting the expectations of customers and consumers globally applies to all of the products we offer. Our production facilities are geared toward delivering safe goods that comply with regulatory standards and with our own strict quality requirements. This is monitored by comprehensive internal and external controls. We also strive to collaborate closely with our suppliers and partners to ensure that premium quality characterizes the entire value chain, from the sourcing of raw materials through to delivery of the final products.
Impact, risk, and opportunity management
We address our quality and safety impacts, risks, and opportunities by meeting food safety standards and taking actions to achieve the commitment set in our Sustainability Plan.
Our material impacts, risks, and opportunities
According to our Double Materiality Assessment (DMA), “Product quality and product safety” is a material topic. We have identified material impacts risks, and opportunities in our own operations and upstream and downstream value chain in relation to this topic.
Food products can impact the health and safety of consumers, and require thorough management and quality controls. Potential health effects on consumers, as well as recalls or withdrawals of products, present reputational as well as financial risks and can lead to significant loss of trust in our brands. We continue to have a strong focus on quality to maintain the overall consumer experience of our products and provide us with a competitive advantage in the market.
Our related policies and documents
To make sure our products meet high food safety standards and are safe for consumption, our production facilities, with the exception of Russell Stover, have certified food safety management systems in place (Food Safety System Certification FSSC 22000). FSSC 22000 is an internationally recognized standard for food safety management systems. The standard emphasizes continuous improvement and risk management in food safety. CEOs and Country Managers of subsidiaries are accountable for compliance with food safety standards. Compliance with the FSSC 22000 standard is assessed yearly by an external certification body.
Beyond the food safety and quality management systems in our production factories, we have established global standards. These include global raw material specifications for our key raw materials as well as quality standards for final products and key production processes. Any changes affecting our global recipes and production processes need approval from our internal International Recipe Committee.
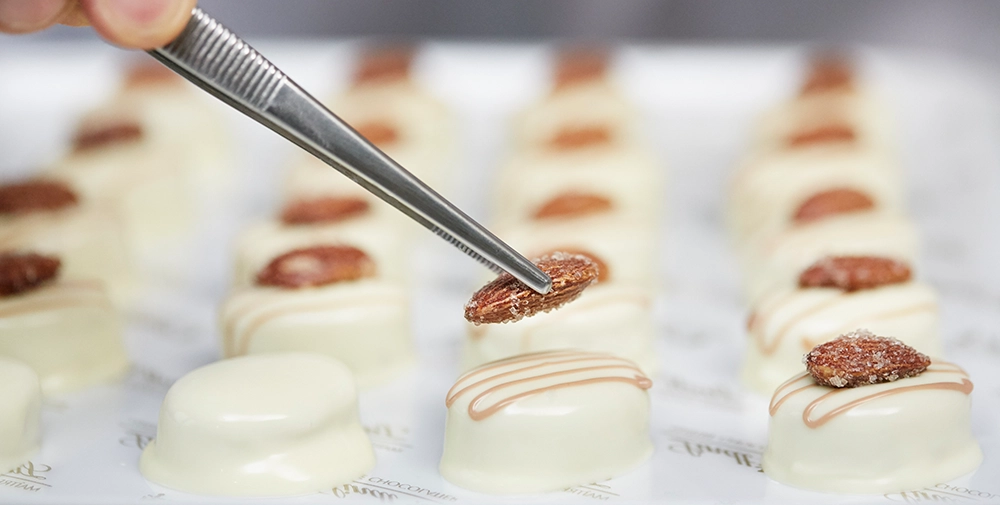
Setting high standards
We aim to ensure high quality along the entire value chain. This involves focusing on food safety, product quality, and execution to ensure that customer and consumer expectations are met with consistent premium quality products and services. We foster a quality culture across all disciplines and levels of the Group and direct our suppliers and service partners to act according to our quality requirements.
Understanding consumer preferences and valuing consumer feedback
Understanding consumer preferences and behaviors drives our product development and enables us to craft impactful marketing strategies. This leads to products that consistently delight consumers and exceed their expectations.
An important part of our development of new product creations is the tasting of recipe prototypes by consumers. Through these tastings our development teams gain valuable insights into consumer requirements and taste preferences.
We value all consumer feedback and suggestions for improvement and offer various channels to contact our consumer service, adapting these to local preferences, e.g., phone, websites, and live chats. Consumers can find contact information on our websites and products. Service procedures are in place to solve and answer consumers’ questions, complaints, and concerns. Consumer service representatives collaborate with internal departments according to defined global standard procedures. We conduct regular surveys to collect feedback in selected countries from consumers who have had interaction with our customer service, and also related to selected topics addressed. This helps us track the performance of our customer service and to continuously improve its quality.
Consumer complaints are investigated, the departments concerned are informed, and aggregated data on complaint reasons is reviewed regularly. The Head of Quality of the Lindt & Sprüngli Group informs Group Management regularly about the consumer feedback and complaints statistics. Consumer feedback statistics constitute important quality performance criteria and are regularly reviewed to adjust quality systems with the aim of reducing the amount of consumer complaints.
Implementing regulatory requirements and scientific findings
Our global network of internal experts identifies new scientific findings, regulations, consumer requirements, and trends that affect our products and production. Several internal expert groups meet regularly to discuss developments. Based on these findings, we review our ingredients, food contact materials, and processes. We adjust recipes where necessary, and work with our suppliers and partners to mitigate potential risks.
Strengthening our quality culture
Lindt & Sprüngli is committed to fostering a strong culture of quality and food safety across all aspects of our business. In 2024, we launched a dedicated global program to further strengthen the Group’s quality and food safety culture. We initiated surveys across our subsidiaries to gain deep insights into our employees’ perspectives ensuring that their feedback translates into meaningful actions that drive continuous improvement. Our approach is fully aligned with the expectations of international standards such as FSSC 22000, reinforcing our dedication to meeting and exceeding global food safety and quality requirements.
Quality inspections and audits
For quality assurance purposes, our production sites undergo unannounced and comprehensive inspections, conducted by external parties. This is overseen by the Head of Quality at Group level and the results are reported to Group Management. Equally important are our regular raw and packaging materials supplier audits to make certain that final products meet Lindt & Sprüngli quality standards.
Metrics and targets
1Product quality and product safety target was specified in line with reporting requirements.
PwC CH