Material topic
- 16 Employee health, safety and wellbeing in own operations
Occupational health and safety
Occupational health and safety (OHS) is vital to our business. We perform best when workplace safety is everyone’s priority and responsibility. Lindt & Sprüngli aims to prevent work-related injuries and illnesses. All of our employees and contractors have the right to a safe working environment that is conducive to good mental and physical health.
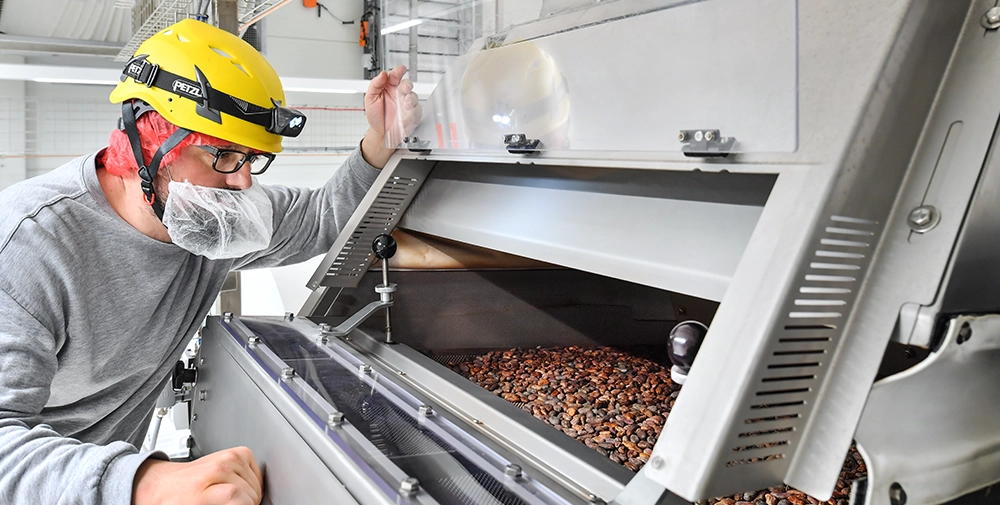
Impact, risk, and opportunity management
We address our health and safety related impacts, risks, and opportunities by implementing actions to achieve the commitment in our Sustainability Plan.
Our material impacts, risks, and opportunities
According to our Double Materiality Assessment (DMA), “Employee health, safety, and wellbeing in own operations” is a material topic. We have identified material impacts, risks, and opportunities in our own operations in relation to this topic.
Healthy and productive employees are the foundation of Lindt & Sprüngli’s business. Physical and psychological integrity is also an unequivocal right of employees. Failure to offer a safe and healthy working environment for all staff and contractors can lead to significant, and in the worst case life-changing, negative personal impacts.
We are mindful that any incidence of not maintaining a safe working environment presents multiple risks. These include reputational damage to our business, legal consequences, reduced productivity, and financial loss. Violations of health and safety standards could result in monetary penalties and costs for corrective actions. High injury rates may indicate weak processes and standards, as well as an immature workplace safety culture, and lead to significant personal and/or reputational harm.
Strong performance on workforce health and safety presents an opportunity, as it can help enhance worker morale and build brand image, which may lead to reduced employee turnover, increased productivity, and strengthened community relations. Maintaining and improving the safety of our facilities overall in turn can help to reduce incident rates, potentially reduce costs, and increase productivity.
Our related policies and documents
Our current approach to health and safety is guided by our Health and Safety Policy, which covers our own workforce. The Health and Safety Policy outlines our commitment to comply with applicable laws, regulations, and industry standards, along with our commitment to providing employee training on health and safety matters.
Our local health and safety management systems enable us to monitor our performance while reducing safety risks. The Lindt Performance Way (LPW) operational excellence program is designed to ensure that our health and safety policies and standards are applied at our production facilities worldwide. The LPW is, and will remain, the basis for driving continuous improvement in this and other areas.
In our Supplier Code of Conduct, we formulate our expectation that our suppliers provide their own employees with a safe and healthy workplace. To learn more about our efforts regarding safe and fair working conditions for workers along our supply chain, refer to the Improving livelihoods chapter. We also depend on distribution partners, wholesalers, and third-party retailers for the sale of our products. However, processes and responsibilities adopted by these sales channels are out of the scope of our health and safety approach.
Safety approach
Our Group Operations team is responsible for Lindt & Sprüngli’s general approach to safety. When it comes to health, we are currently evaluating how we can include the topic in our updated approach in the future. The current approach is implemented by our production facilities, and overseen by Group Management, which receives annual updates. The management teams of local Lindt & Sprüngli production subsidiaries and facilities are responsible for tracking performance on a monthly basis and for developing relevant and specific working procedures and practices to meet local regulatory and Group requirements. We plan to improve and further standardize this approach across all Lindt & Sprüngli subsidiaries. In addition, we will embark on a long-term immersive program to improve the safety culture at all our facilities around the world.
Designated health-and-safety employees at our production sites work to improve the processes and procedures necessary for a safe working environment. They conduct health and safety self-assessments, identify hazards and risks, and investigate incidents. Each Lindt & Sprüngli subsidiary has a system in place for employees to report accidents, unsafe conditions, and near-miss incidents. Employees are encouraged to identify and report workplace hazards and risks, so that we may better understand the root cause of incidents and take preventive action. Each site is responsible for training its employees on OHS topics to support their site-specific needs.
In 2022 and 2023, we conducted a global health and safety audit in all Lindt & Sprüngli subsidiaries and departments. As part of the audit, we comprehensively and systematically assessed our processes and performance globally in 2024. Based on the observations from this assessment, we will consider updates to our approach of managing health and safety. Various policies, processes, and procedures will be reviewed, and in some cases amended in the short and medium term, to prepare for an aligned approach founded on the ISO45001 standard. We will implement a global health-and-safety management system in the coming years, ensuring a unified approach.
We anticipate to start with the design of a new Group-wide health and safety program in the second half of 2025. The new Safety Transformation and Asset Risk (STAR) program will be based on a zero incidents principle, meaning that every employee returns home in good health each day. The program will also focus on building a strong safety culture throughout the organization, and ensuring that everyone adopts and promotes a safety-driven culture. Ultimately, these two commitments support our vision of “Safety is our first ingredient”.
To achieve this vision, we plan to deploy various programs over the years to come. It will take some time to enable this shift in our approach and to ensure deep integration and understanding amongst all employees.
In the meantime, we continue to use existing practices, such as activity-based risk assessments and incident investigation, to improve our performance. Our new approach will focus on improving these and many other processes.
Metrics and targets
3.59
Rate of lost-time accidents
(No. of lost-time accidents per 1 million working hours)
In 2024, we required all Lindt & Sprüngli subsidiaries and departments to record incidents in one new and centrally-coordinated system based on a revised globally-aligned definition for the first time. We, therefore, have no comparable historical data on our performance.
We now report work-related accidents across all activities, including production (e.g., factory) activities and non-factory activities (e.g., in shops or offices). In 2024, there were 213 recordable work-related accidents in total, of which 92 resulted in lost time. There were three high-consequence work-related injuries. Just over 75% of total incidents occurred in our production operations. As part of the anticipated change to our health and safety management processes, we will prioritize improved risk management in those processes.
PwC CH